What Is Laminated Tube& How To Customize in Factory
Laminated tubes are made from multiple layers of polymers and other materials that are pressed together using an aluminum or plastic barrier inserted between the inner and outer layers of the tube. Because of the special manufacturing method, laminated tubes make an excellent barrier to protect products and thus extend shelf life.
Laminated tubes are becoming increasingly popular in several verticals such as food, pharmaceuticals, and cosmetics, and there is a tremendous demand in terms of volume in the industry for laminated tube packaging.
What is the Laminated Tube
The barrier layer is the most critical component of a laminated tube and it can be made from a variety of materials, the two most common being aluminum and EVOH film. In this section, we will focus on three common types of tubing and the differences between them.
1. ABL Tube (Aluminum Barrier Laminated Tube)
ABL tubes use aluminum foil as a barrier layer, which protects the contents from light, air, moisture, and flavors in the environment. ABL tubes are often used for toothpaste, gels, creams, etc. Another characteristic of ABL tubes is that they retain their shape after being squeezed and do not regain their original shape once squeezed. So you can clearly know how much product has been used.
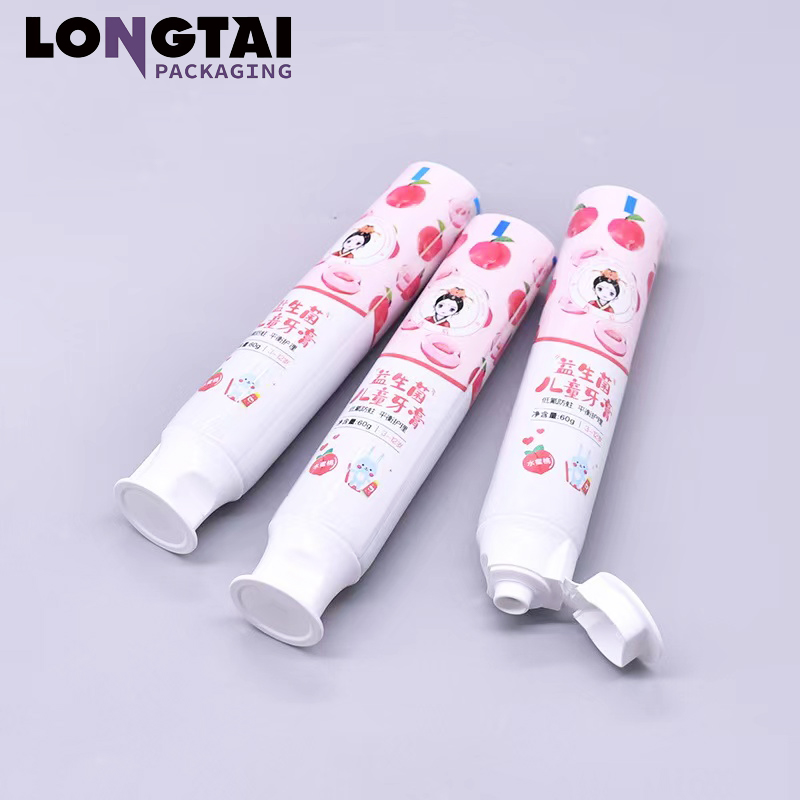
2. PBL Tube (plastic barrier laminated tube)
PBL tube, a plastic barrier laminate tube consists of EVOH (ethylene vinyl alcohol) film as a barrier layer, which can effectively prevent oxidation of the product. Making PBL tubes starts by layering EVOH film with other plastic materials to make a sheet, then this sheet is cut into a suitable shape and rolled into a tube. Immediately afterward, the longitudinal edges of the tube are welded together to form the tube body. Finally, the tube body is sealed to the tube shoulder. one of the key differences of PBL tubes is their ability to retain their original shape and to quickly return to their original shape even after being squeezed hard.
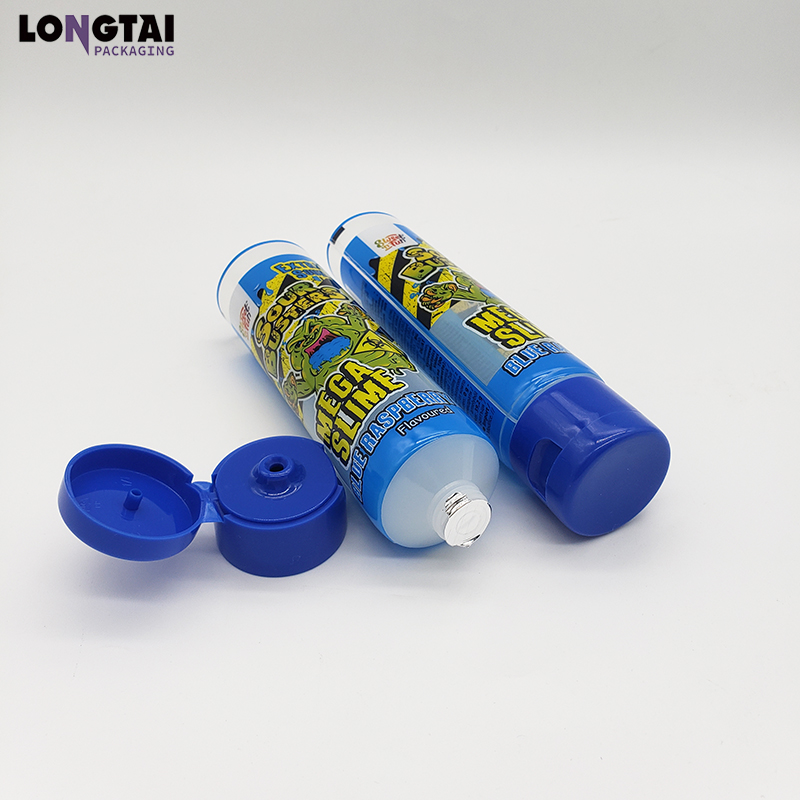
3. COEX Tube (co-extruded tube)
Similar to PBL tubing, co-extruded tubing uses EVOH film as a barrier layer. The difference is that COEX tubes are not made by cutting, rolling and sealing steps, but have extruded plastic layers made. What you end up with is a tube without seams. Like the PBL tube, the extrusion is able to return to its original shape.
Benefits of Laminated Tube Packaging
Laminated tubes are highly protective against light, air and moisture, with the advantages of plastic and barrier properties with metallic characteristics. In the past few years, the cosmetic industry has surfaced as a multifunctional market. These tubes maintain the integrity of the product by providing features such as moisture retention. They are used to package cosmetic products such as creams, skin care products and cleansers.
Some of the properties are as follows.
- Hygienic and safe to squeeze
- Moisture, light and aggressively resistant
- Has a plastic feel and aluminum characteristics
- Customizable colors, designable and shelf appeal
- Easy and smooth to use
How To Customize Cosmetic Tube in Factory? Long-Tai Custom Process
If you’re looking to buy either of the tubes, then we’ve got you covered. From packaging customize molding, graphic design, printing services, labeling, filling, and end-to-end services to packaging containers for the personal care, cosmetic, care and hotel industries.
- Custom Mould
- Graphic Design Packaging Design
- Printing Service
- Sourcing & Shipping Service
Long-Tai Cosmetic Tubes Custom Process
1. Cosmetic Tube Extrusion
The first stage of making cosmetic tubes is extrusion, where the raw plastic and masterbatch are mixed together. During the extrusion process, different dies can also be selected to make different shapes, and then cut into different shapes and sizes.
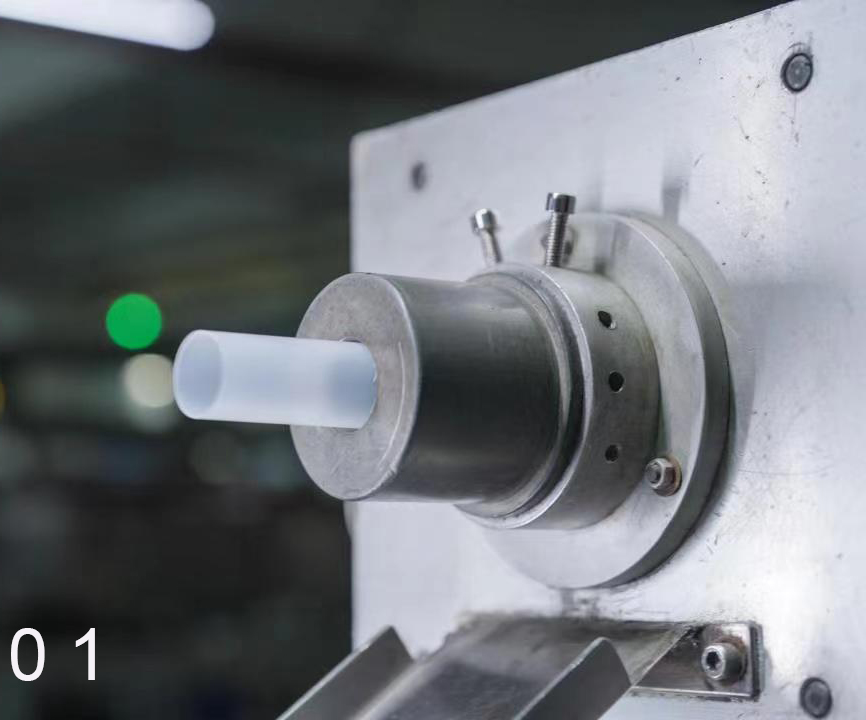
2. Auto Heading
There are three head processes. One is by injection molding, where the head is attached to a plastic sleeve. The other is an additional compression method where the head is shaped with a donut of melted resin material in addition to the traditional method.
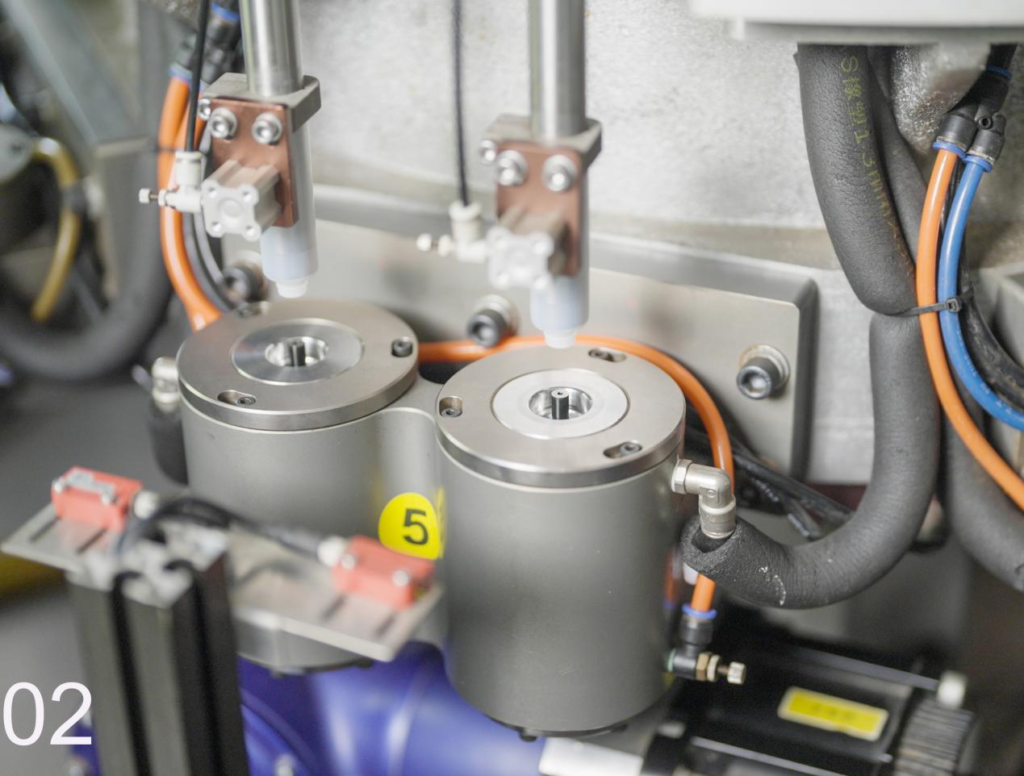
3. Offset Printing
Offset or offset lithography is a printing technique that transfers ink from the printing plate to a rubber roller and then to the material to produce high-quality images and designs.
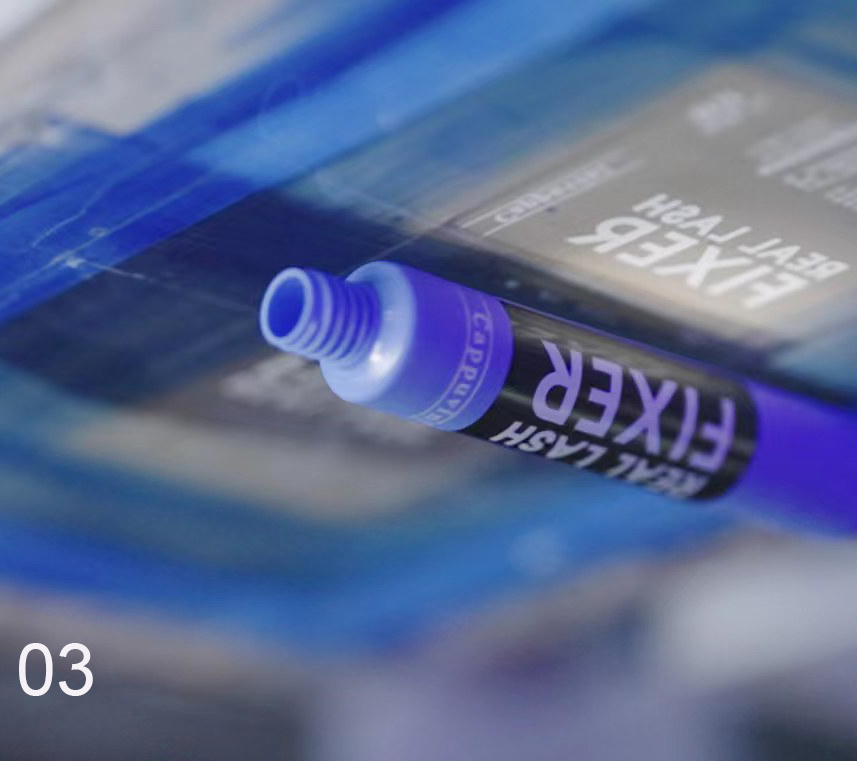
4. Laminated Tube Printing
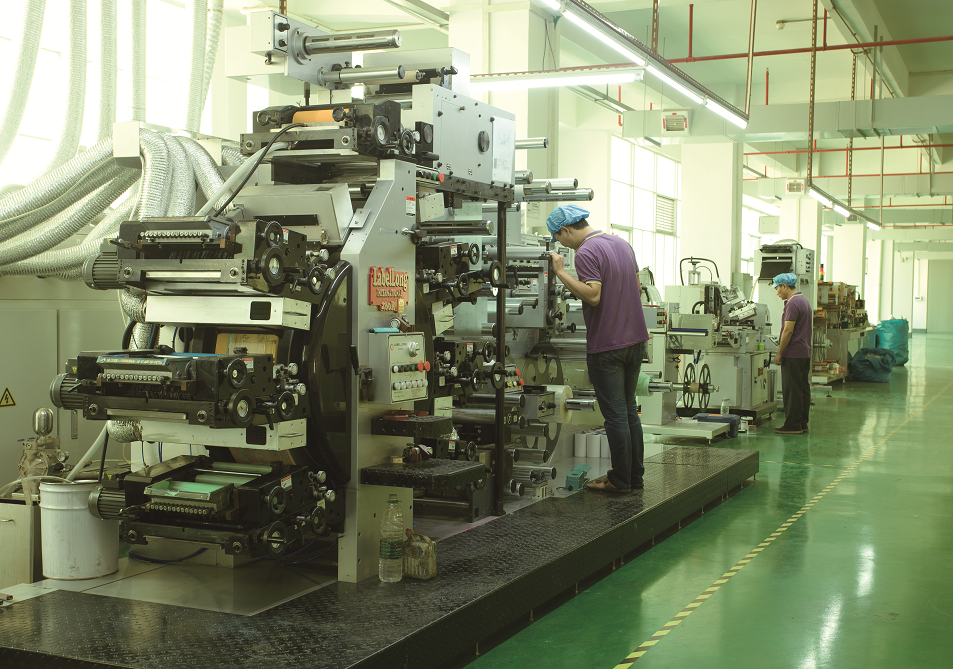
5. Silk Screen Printing
The best process for labeling cosmetic tubes is screen printing, and labels made through screen printing techniques are less prone to wear and tear.
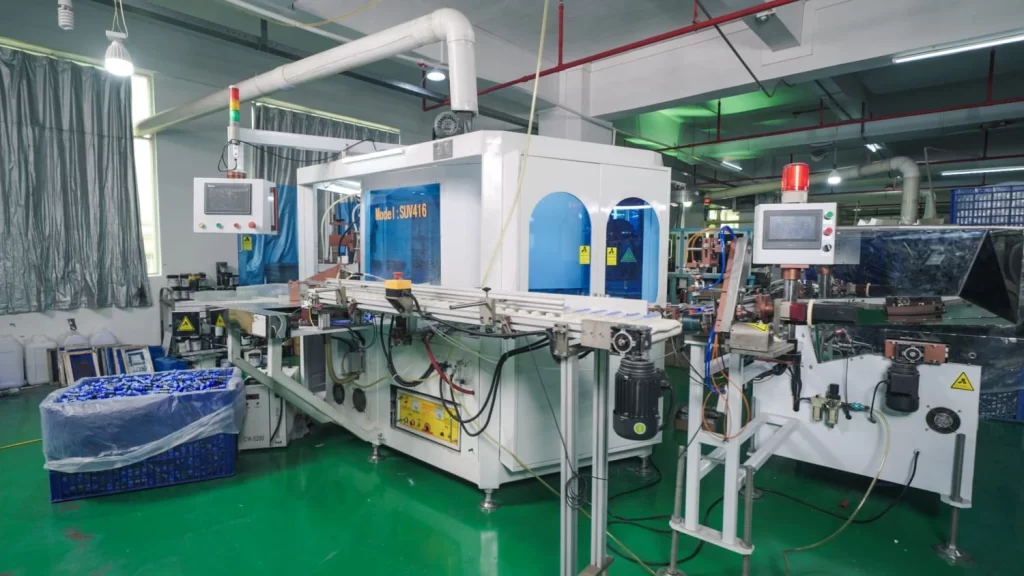
6. Hot Stamping
The marking cycle begins when the stamping machine engages the heated die or type with the foil and transfers the ink from the foil carrier to the part to be marked.
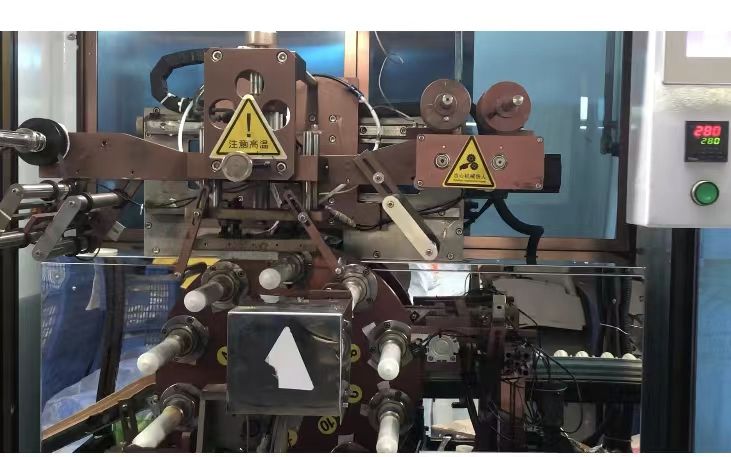
7. Welding
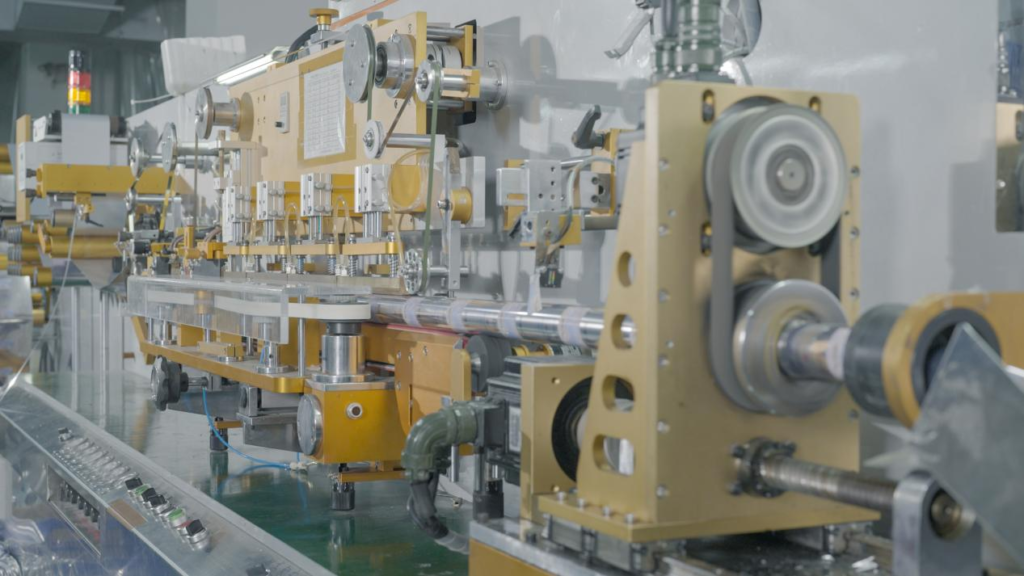
8. Foil Sealing and Cap Assembling
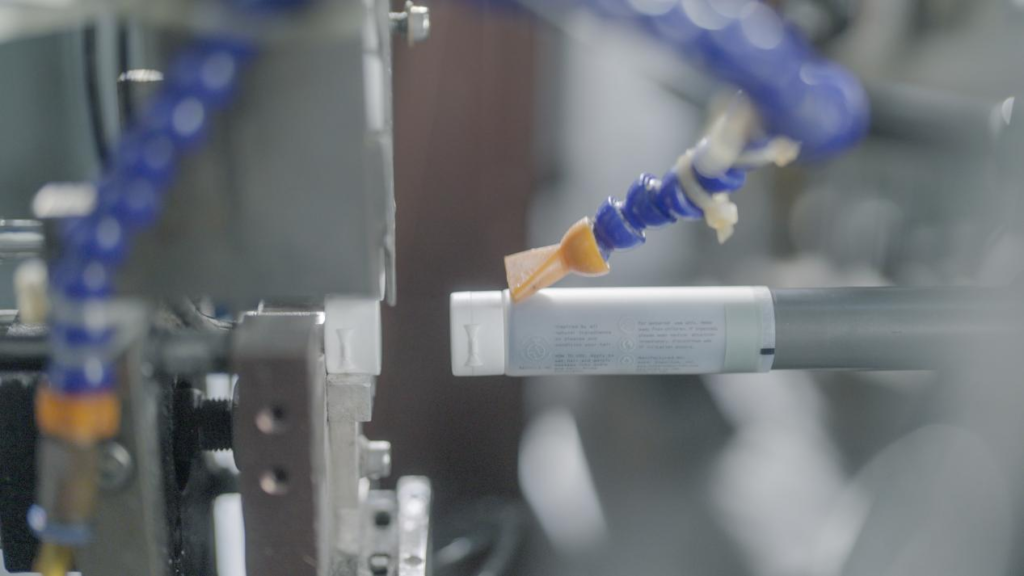
9. Tail end Selding
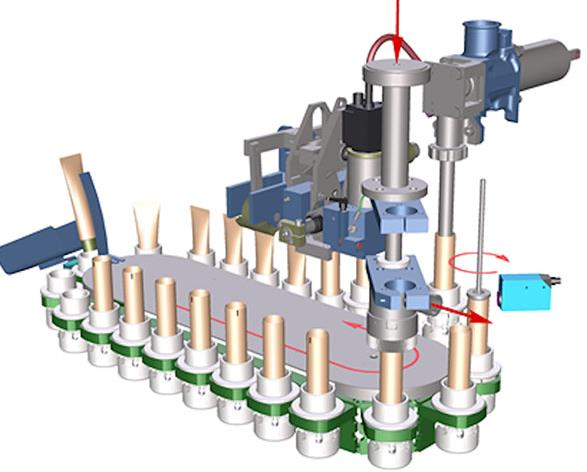
10. Test for Cosmetic Tube
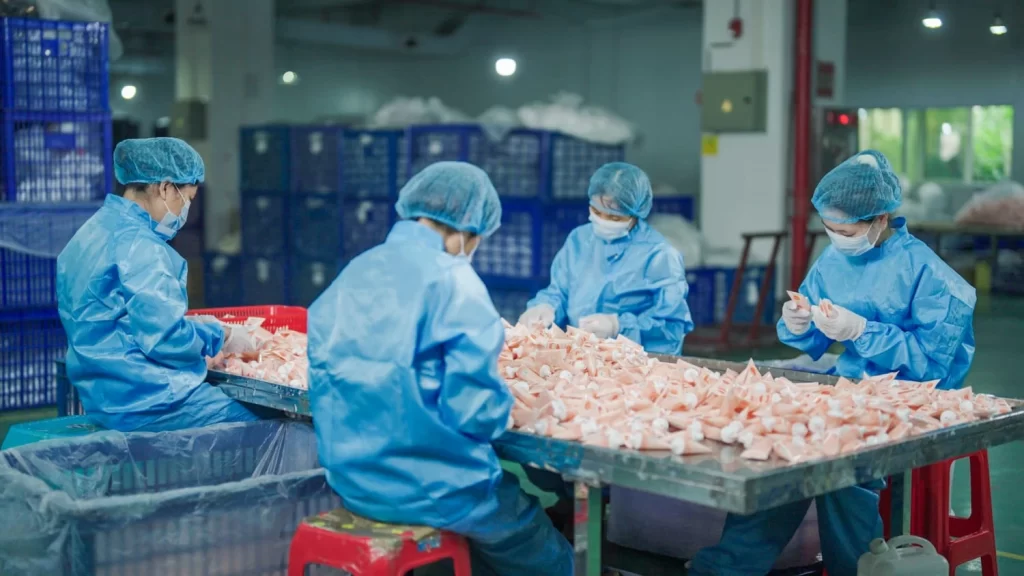
11. Teams and Products
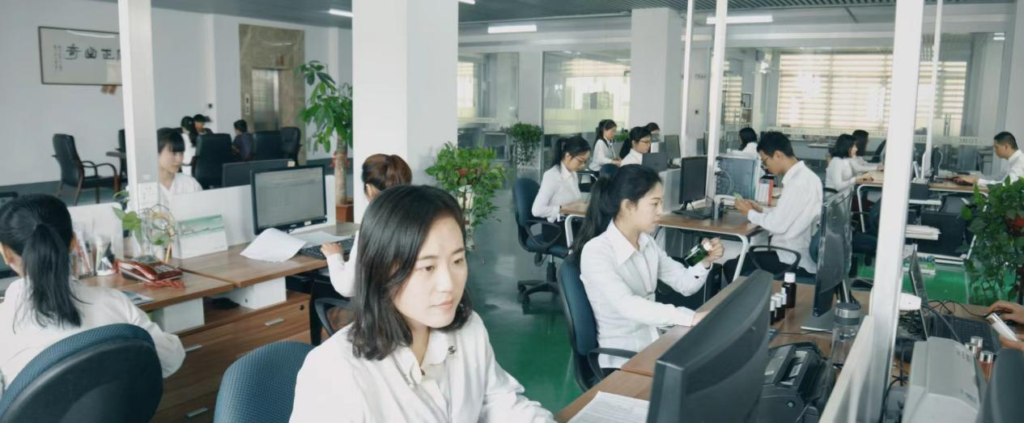
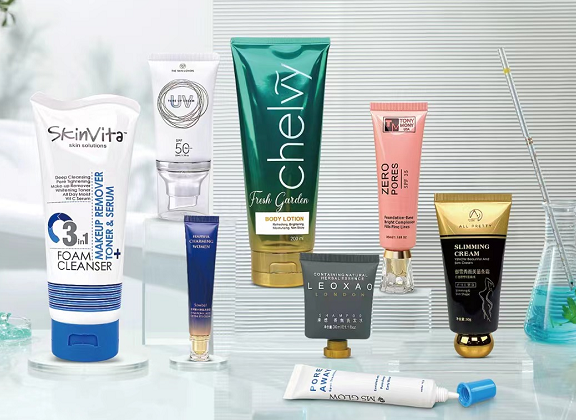